1. Initial Inspection
As soon as equipment is returned, our team performs a thorough visual inspection. We check for any signs of damage, wear, or missing components. This includes examining connectors, screens, cables, and casings to ensure there’s no external damage that could affect the equipment's performance.
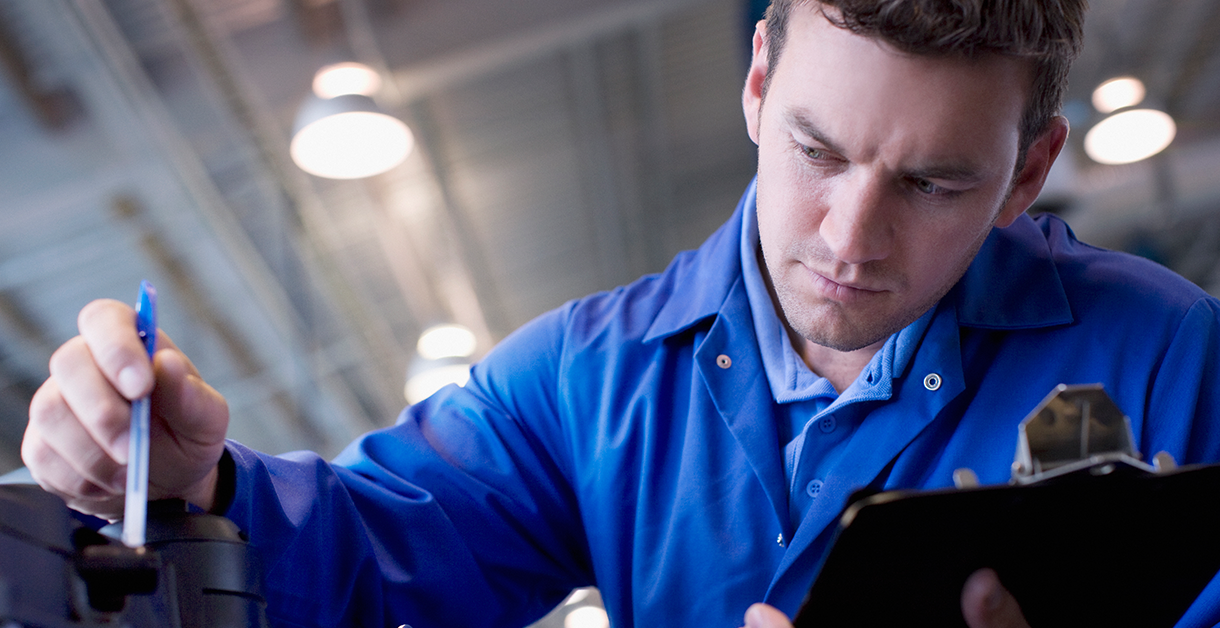
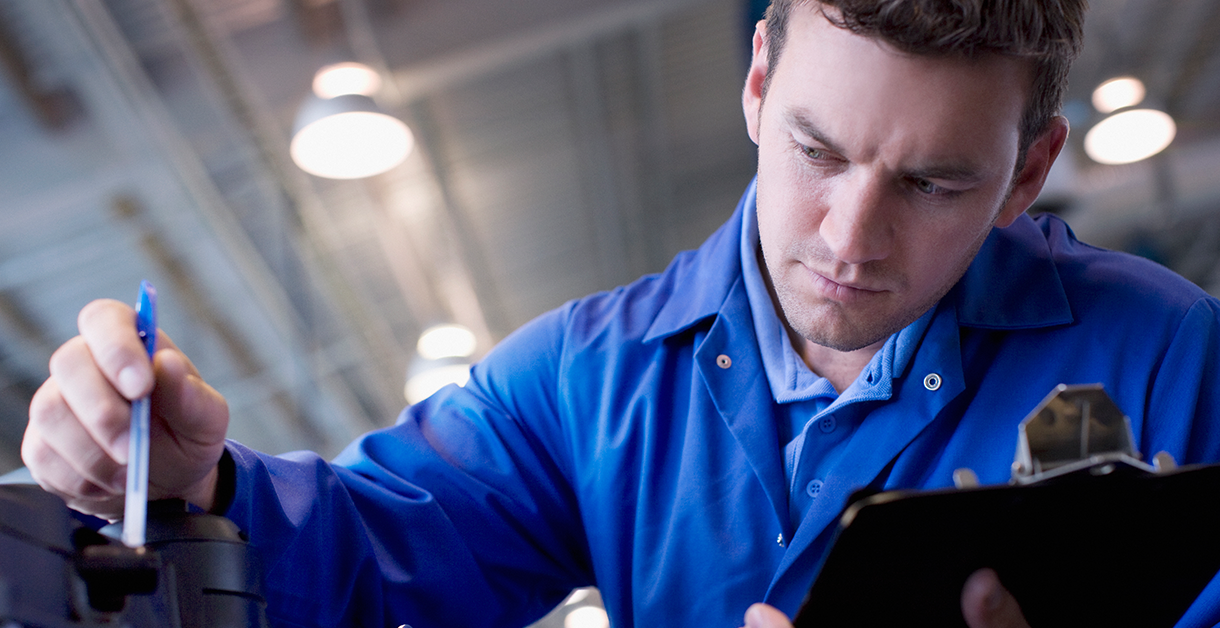
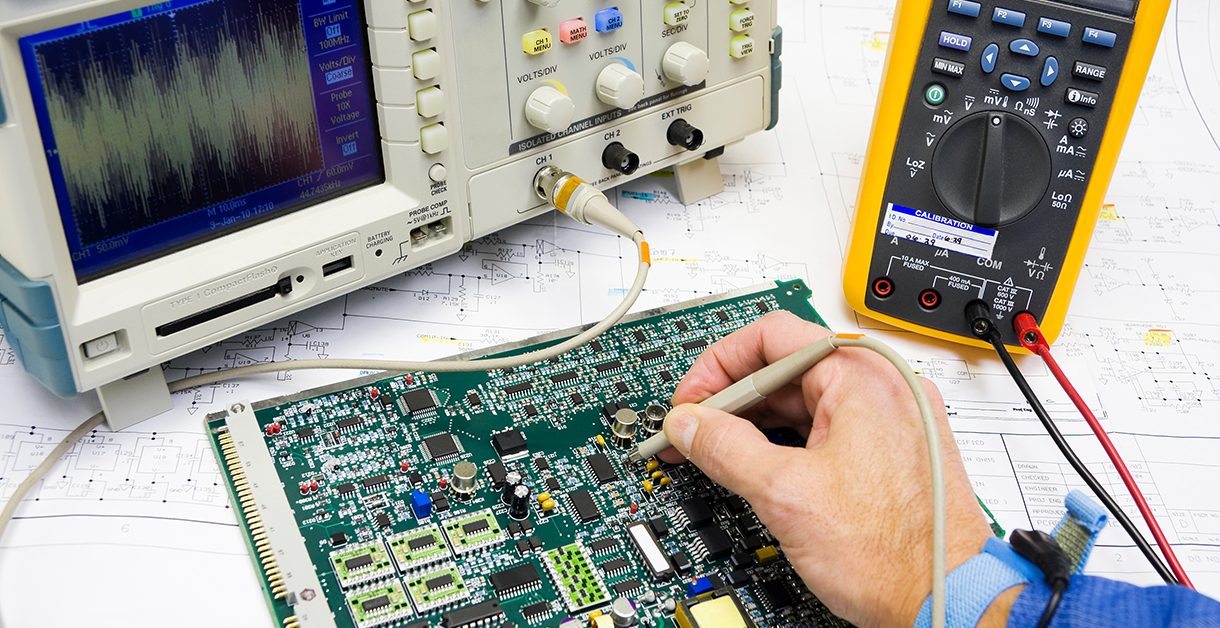
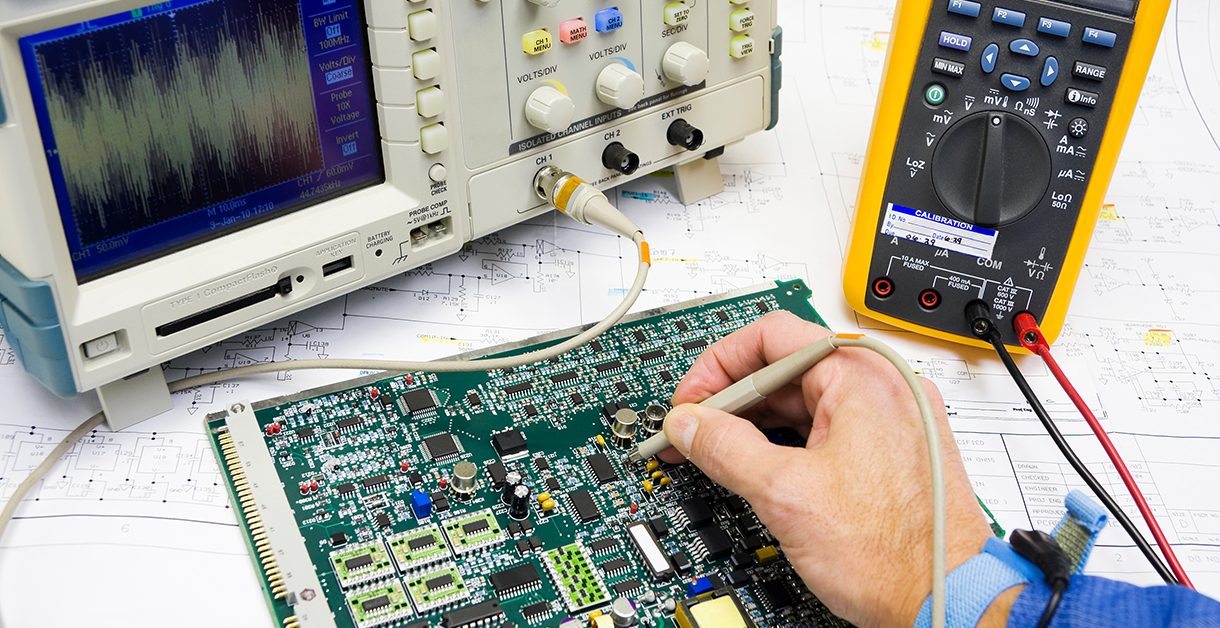
2. Comprehensive Functionality Testing
Next, we move to the technical checks. Each piece of equipment undergoes a full operational test to verify that all functions are working as intended. This includes running the equipment through various operating modes and testing key features such as:
- Accuracy of measurements
- Calibration status
- Signal integrity (where applicable)
- Data recording and output functions
This is done using manufacturer-recommended procedures and test standards to ensure precise results.
3. Calibration Check (and Recalibration if Needed)
Accurate calibration is crucial for test and measurement equipment. If the equipment is due for recalibration (based on manufacturer guidelines or usage), our certified technicians perform a calibration check using NATA traceable standards. If necessary, the equipment is recalibrated to ensure it meets factory specifications for accuracy.
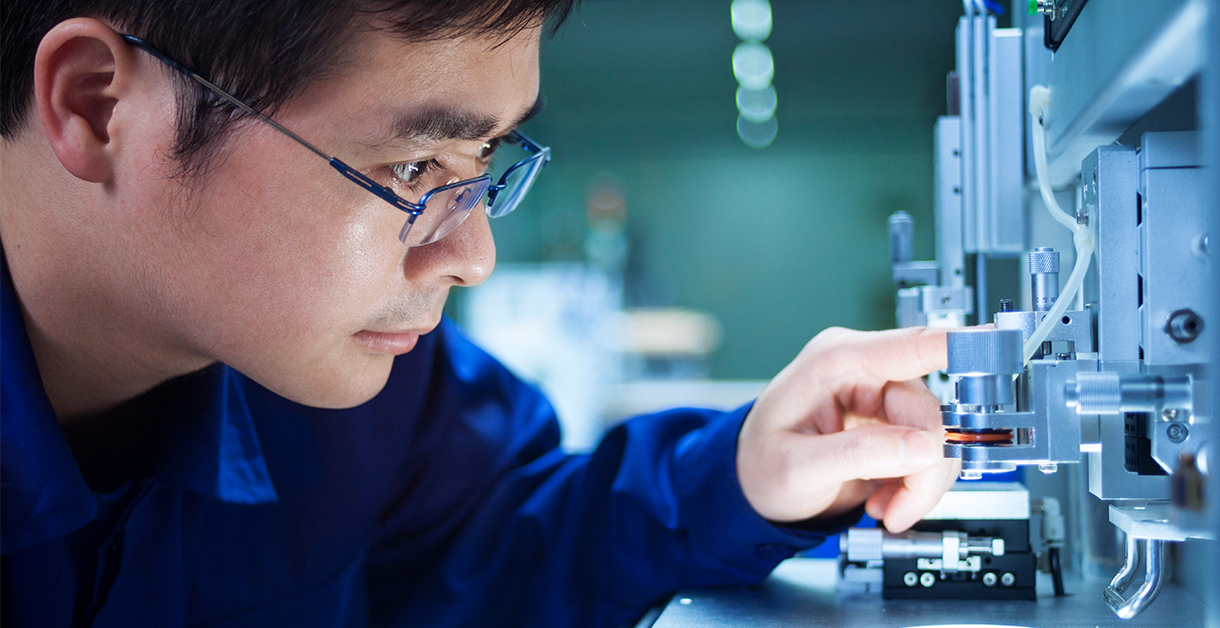
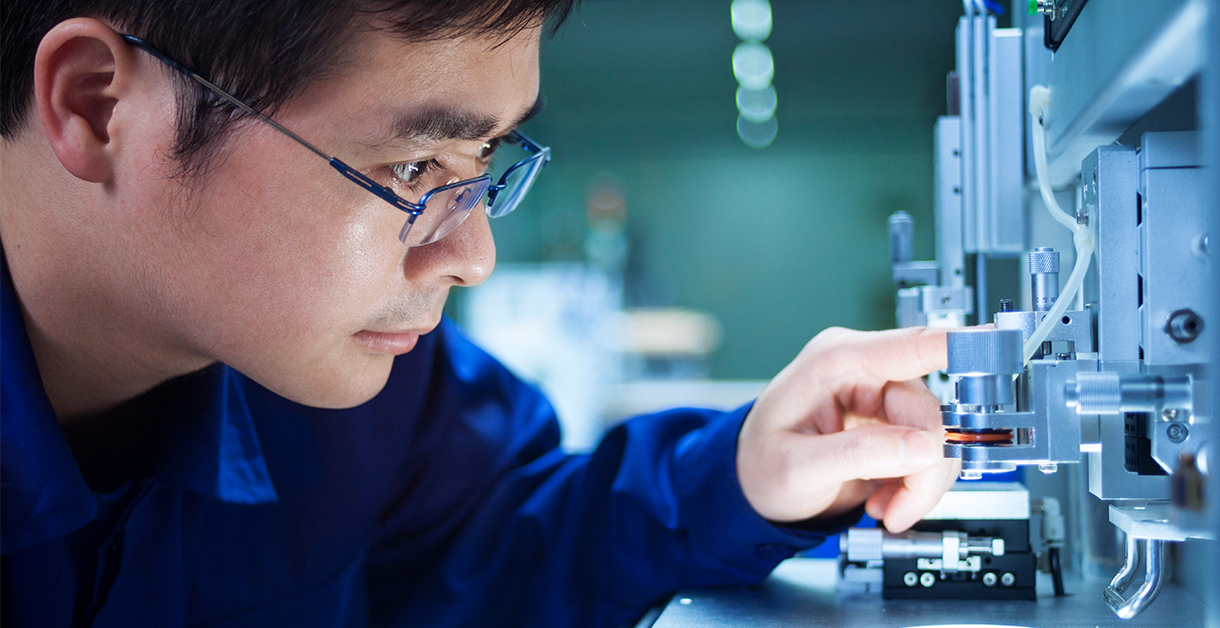
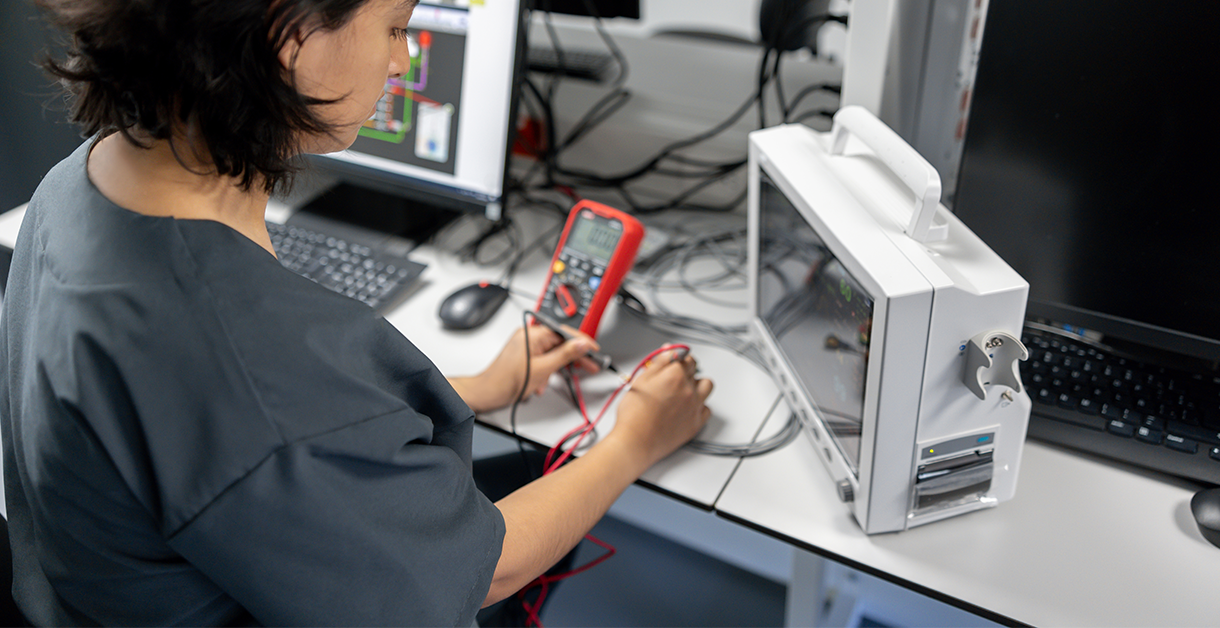
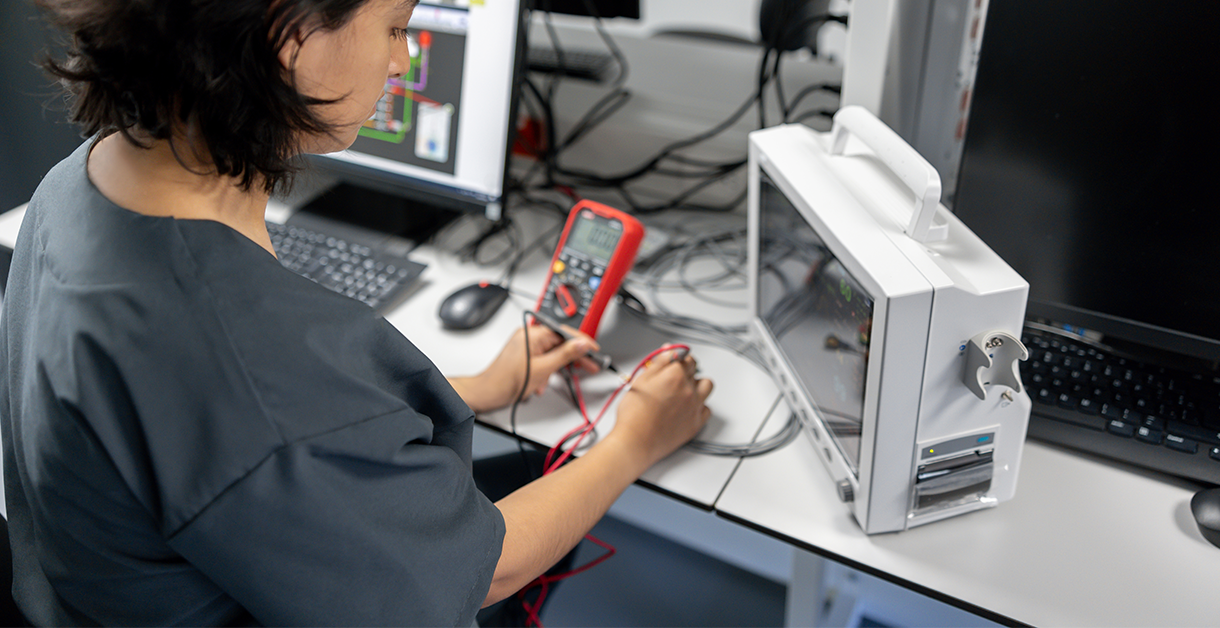
4. Cleaning and Sanitisation
For equipment that requires handling, we thoroughly clean and sanitise all touch surfaces. This step ensures not only hygiene but also removes any residues that could interfere with the equipment's performance, such as dust or oil.
5. Final Quality Control
Before being placed back into our inventory for rental, the equipment goes through one last quality control check. This ensures that everything, from accessories to performance, is in perfect order. Any issues flagged during earlier steps must be resolved before this final sign-off.
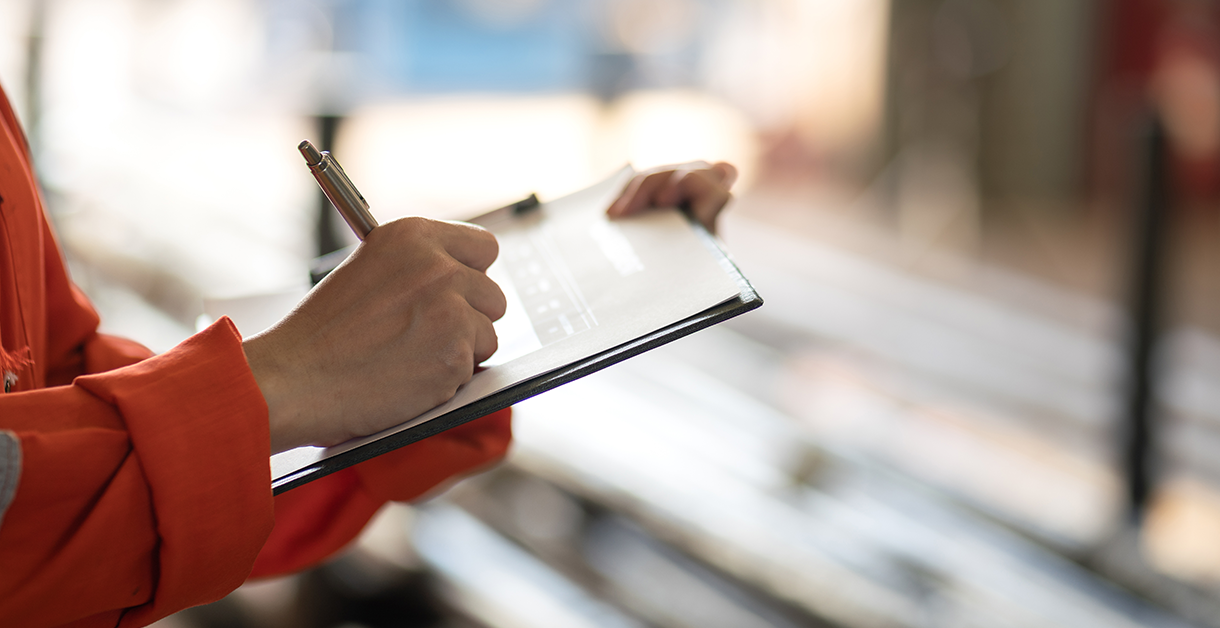
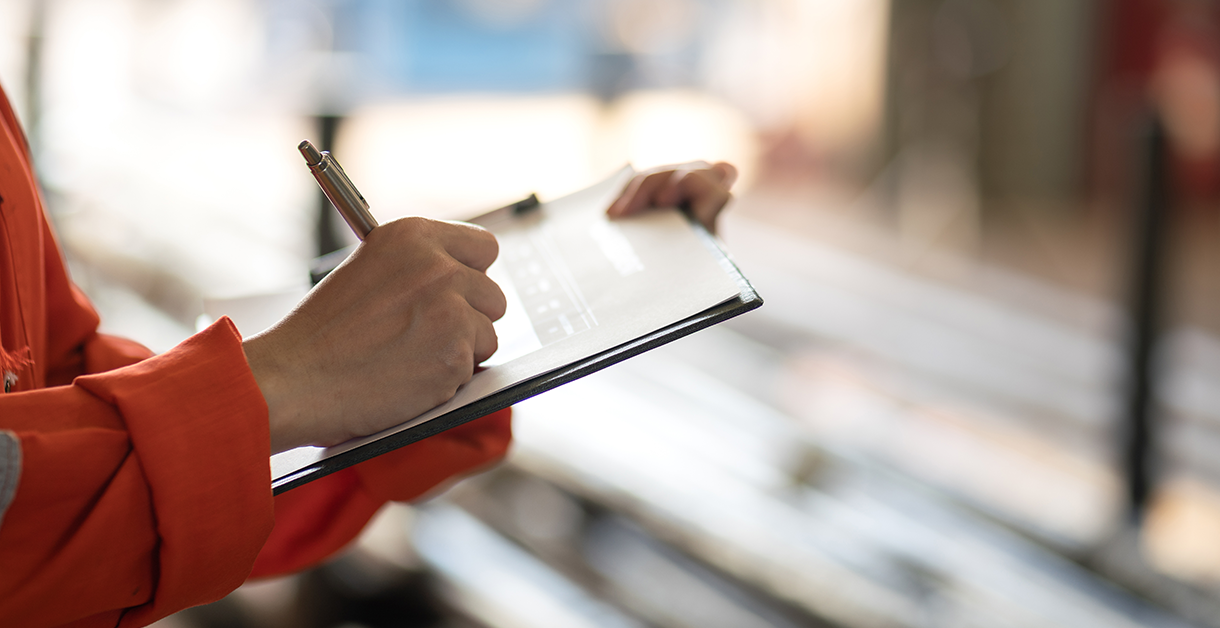
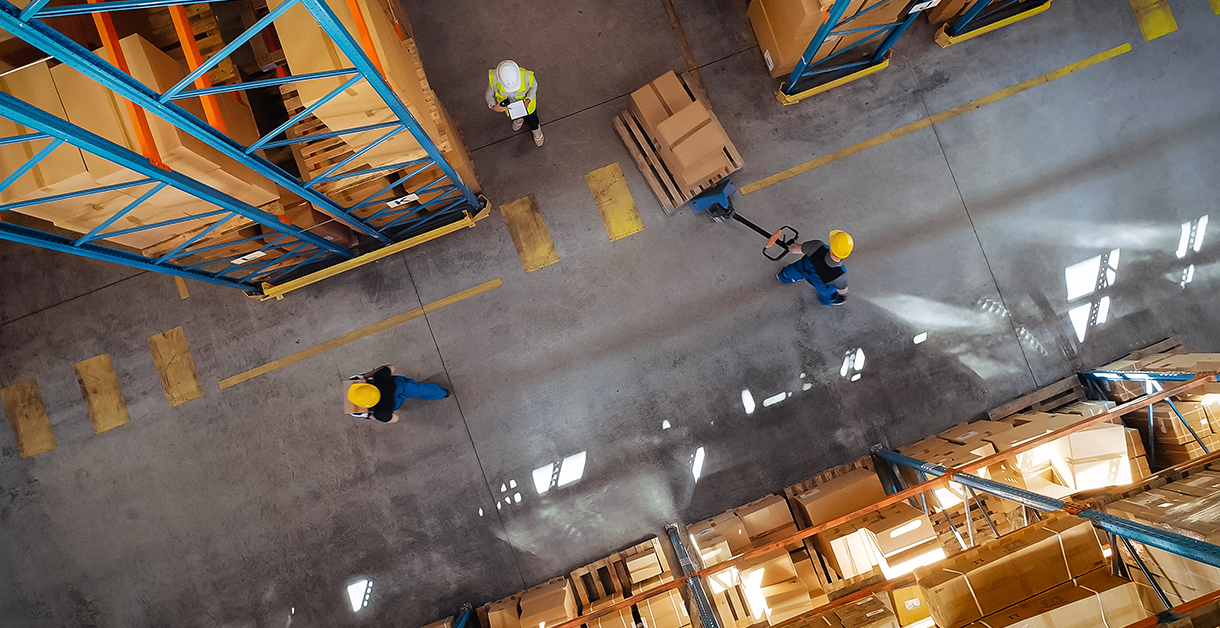
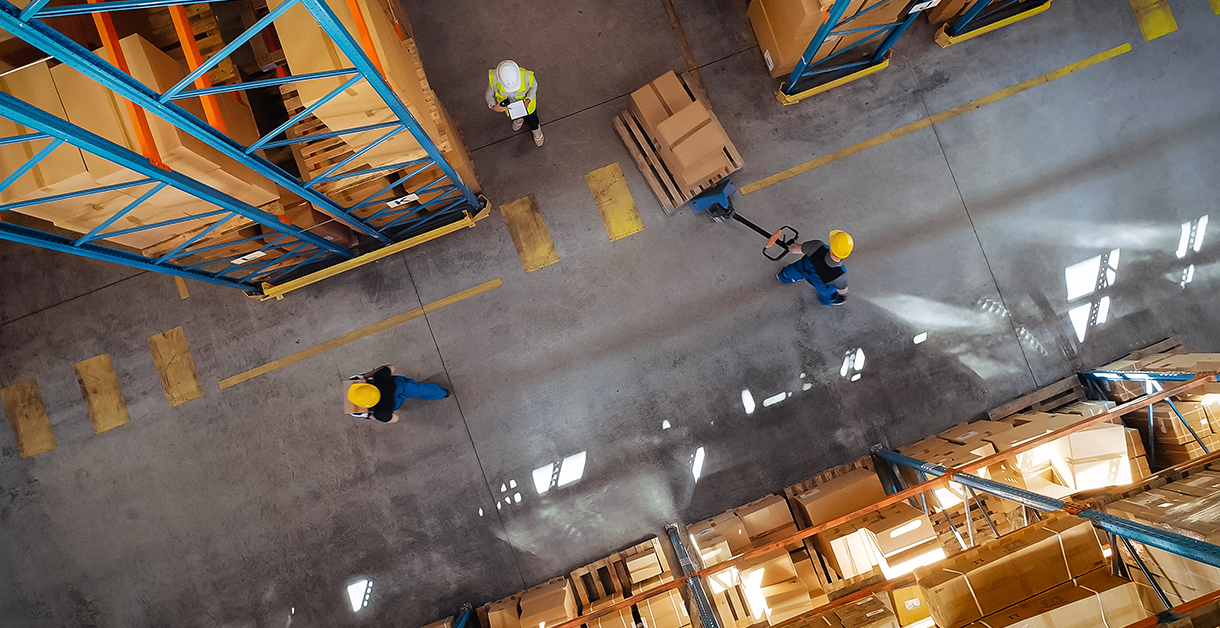
6. Packaging for Next Use
Once the equipment has passed all checks, it’s carefully packed with all required accessories, manuals, and cables. This ensures that the next customer receives the equipment in the same reliable condition.
Confidence in Every Rental
By following this post-rental process, we guarantee that every piece of test and measurement equipment you rent from us will perform as if it were brand new. TechRentals commitment to quality gives you the confidence to rely on our products for your critical testing needs.